Hi dear friends welcome to our blog. If your Washing Machine Pausing.
So Don’t worry this is a common issue.
In this guide, we explain 15 common reasons for this problem with unique solutions. So let’s start now.
Why Is My Washing Machine Pausing
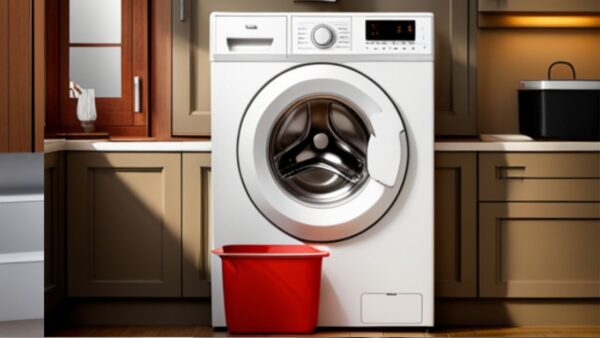
1. Overloaded Drum
Cause
When too many clothes are added to the washing machine, it results in an overloaded drum.
This causes the machine to pause as it struggles to distribute the load evenly during its cycle.
Overloading can also put undue stress on the motor and other components, leading to potential damage or malfunction.
Solution
To rectify this issue, ensure that you are not exceeding the load capacity recommended by the manufacturer.
Consider doing smaller loads and evenly distributing the clothes within the drum to prevent imbalance.
Regularly maintaining and checking your machine’s load can prolong its lifespan and promote efficient performance.
2. Unbalanced Load
Cause of Unbalanced Load
An unbalanced load usually refers to an uneven distribution of load on a power system.
This situation often arises due to uneven distribution of electrical loads across the three phases of a power system.
It can cause serious problems, including overheating of equipment, increased energy losses, and possible system failure.
Overloading one phase while others remain underutilized can lead to this unbalance, causing substantial harm to the system’s overall performance and efficiency.
A Solution to Unbalanced Load
Addressing an unbalanced load requires the redistribution of power to achieve equilibrium across all phases.
This includes assessing the power requirements of different devices and strategically allocating these across the phases to ensure an even distribution.
Regular monitoring and maintenance of the system are also critical.
Implementing a load-balancing policy and utilizing load-balancing equipment can significantly mitigate the effects of unbalanced loads.
Regularly reviewing and adjusting the distribution, considering the fluctuating needs, can also help in preventing unbalance from occurring in the future.
3. Debris in the Drain Pump
Cause
Drain clogs are often caused by an accumulation of small items and debris in the pump.
This can be anything from food particles, hair strands, and small toys, to lint from clothes. The debris gets caught in the pump, preventing water from draining effectively.
This could lead to your drain pump becoming noisy, or worse, completely stopping working.
Remember: Even the smallest items can cause significant problems in your drain pump.
Solution
The primary solution to debris in the drain pump is regular cleaning and maintenance.
Ensure you periodically check the pump for any trapped items and remove them promptly.
If the pump is severely clogged, it may be necessary to disassemble it for thorough cleaning or even replace it.
Note: Regular check-ups and prompt removal of debris can extend the lifespan of your drain pump.
4. Tripped Circuit Breaker
Cause
A circuit breaker trips, or shuts off the electrical flow, to protect the circuit from overheating and causing damage—even possibly an electrical fire.
This usually occurs when too many appliances or electrical devices are operating at once on the same circuit.
Overloading creates an excessive electrical demand on the system, resulting in an automatic trip.
Remember, circuit breakers are safety devices designed to prevent wiring overheating and potential fire hazards.
Solution
To reset a tripped circuit breaker, first, turn off all the appliances on the overloaded circuit.
Then, locate your electrical panel and find the breaker that has moved to the neutral position or is completely off.
Push the breaker firmly into its correct place until you hear a clicking noise. Always ensure your hands are dry and you are standing on a dry surface for safety while handling electrical panels.
However, if the breaker continues to trip, it’s time to consult a professional electrician to investigate the problem.
Repeated tripping indicates a deeper issue that requires professional attention.
5. Faulty Lid Switch
Cause
The lid switch indicates to the washing machine when it’s safe to proceed to the next cycle. If it’s faulty, the washer may not proceed beyond filling or draining.
Common symptoms of a faulty lid switch include the machine not spinning or the machine stopping mid-cycle.
Solution
The solution to a faulty lid switch is typically replacement. Switch replacement should always be done by a professional or someone familiar with appliance repair.
Incorrect installation may lead to other issues or even pose a safety risk. Before calling a repair service, check if the issue is simply due to a loose switch.
If it’s firmly in place and still not functioning, it’s time to seek professional help.
6. Malfunctioning Water Inlet Valve
Cause
The malfunctioning of a water inlet valve can be caused by various factors. It could be due to a buildup of minerals or sediment, which hinders the free flow of water.
Alternatively, the issue could stem from mechanical failure such as a broken part, or general wear and tear over time.
This can lead to irregular water flow or a complete shutdown of the system.
Solution
Fixing a malfunctioning water inlet valve often involves cleaning or replacing the valve.
If mineral deposits or sediment are the issue, a thorough cleaning can help restore functionality.
However, if the problem is due to mechanical failure or wear and tear, it is usually more cost-effective to replace the valve entirely.
Always consult with a professional plumber to ensure the correct remedy is applied.
7. Broken Drive Belt
Cause
The drive belt, which plays an integral role in operating various engine accessories like the alternator, water pump, and air conditioning compressor, can fail due to a variety of reasons.
Frequently, these failures arise from age and excessive usage, leading to the belt material deteriorating and eventually snapping.
Poor tension adjustment and misalignment of the pulley system can also cause premature belt wear and tear.
Solution
When it comes to a broken drive belt, the remedy is straightforward – it needs to be replaced.
It’s important to ensure the correct belt tension and alignment during the replacement process to avoid premature failure.
Further, regular inspections for signs of wear or damage should be part of your routine vehicle maintenance.
Lastly, if your vehicle has been operating on the same drive belt for a prolonged period, consider replacing it proactively to avoid unexpected breakdowns.
8. Damaged Motor Coupler
Cause
A motor coupler is a critical component in a washing machine that connects the motor to the transmission.
Over time, due to normal wear or overloading, the motor coupler may become damaged leading to problems in the washing machine’s operation.
This will often manifest as a machine that spins irregularly or doesn’t spin at all.
Solution
The solution to a damaged motor coupler is relatively simple: replacement of the part. Turn off and unplug the machine before beginning.
It’s best to consult your washing machine’s manual for specific instructions, but typically, the process will involve removing the cabinet of the machine, detaching the pump, motor, and then the motor coupler itself.
Once the old coupler is removed, install the new coupler and reassemble the machine.
Check the machine’s operation by running a small load to ensure the issue has been resolved. Remember, safety is paramount when performing any maintenance on electrical appliances.
9. Worn Out Clutch
Causes of a Worn-Out Clutch
The principal cause of a worn-out clutch is frequent or harsh driving practices, such as aggressive acceleration or abrupt gear shifting.
This constant friction between the clutch plate and the flywheel eventually leads to wear and tear.
Furthermore, a clutch can wear out prematurely due to oil leakage from the engine or gearbox which contaminates the clutch plate.
Proactive maintenance and adopting smoother driving techniques can significantly prolong the life of the clutch.
Solutions for a Worn-Out Clutch
The most effective solution for a worn-out clutch is replacement. While adjusting the clutch can offer temporary respite, it does not provide a long-term solution.
It’s important to replace the entire clutch assembly, including the clutch plate, pressure plate, and release bearing.
Be sure to choose high-quality replacement parts to ensure longevity and performance. Regular vehicle servicing can also help detect early signs of clutch wear and prevent further damage.
10. Failure of the Timer
Cause
The failure of the timer can often occur due to electrical issues or mechanical wear and tear.
It might be caused by a faulty wiring connection, a burned-out timer motor, or a broken gear. If the timer is not advancing, it could be due to a problem with the timer motor itself.
Solution
To resolve a timer failure, check for any visible signs of damage or wear on the timer’s parts.
If the timer motor is not functioning, a replacement of the timer may be necessary.
Always ensure that all wiring connections are correct and secure. It’s essential to consult with a professional technician if you are not comfortable doing these repairs yourself.
11. Blocked Filter
Cause
The blockage of a filter is primarily caused by the accumulation of impurities, such as dust, dirt, or even organic matter over time.
This is common in systems like water filtration, air conditioning, or fuel systems in vehicles where filters are utilized to eliminate unwanted particles.
Regular usage without maintenance is a major contributor to filter blockages and can result in reduced efficiency, and in severe cases, damage to the system.
Solution
To resolve a blocked filter, the first step is to remove and inspect the filter, often following specific instructions provided by the manufacturer.
If the blockage is not severe, cleaning the filter might suffice. However, if the filter is significantly blocked or damaged, it may require replacement.
Regular inspection and maintenance are key to preventing and addressing blocked filters, ensuring the longevity and efficiency of the system where the filter is used.
12. Problems with the Control Board
Cause
The primary cause of issues with the control board often stems from electrical malfunctions which may be due to power surges, short circuits, or improper installation.
Repeated power surges can severely damage the control board, leading to its inability to perform optimally.
Furthermore, short circuits can cause unexpected system behavior, while shoddy installments may cause loose connections that interfere with the board’s operations.
Solution
Addressing control board malfunctions requires a systematic approach. Initially, it’s crucial to conduct a thorough diagnosis to pinpoint the exact cause of the problem.
This may involve checking for loose connections, assessing for possible power surges, or looking for signs of short circuits.
Once the problem is identified, corrective measures can be undertaken.
This might include replacing damaged components, tightening loose connections, or installing surge protectors to safeguard against power fluctuations.
In severe cases, it might be necessary to replace the entire control board.
13. Faulty Water Level Sensor
Cause
The most common cause of a faulty water level sensor is usually due to accumulation of dirt, debris, or mineral deposits on the sensor.
This residue can interfere with the sensor’s ability to accurately determine the water level.
Another possible cause could be wiring issues or a malfunction in the control board.
Solution
To rectify a faulty water level sensor, begin by cleaning the sensor to remove any accumulated dirt or deposits.
If cleaning the sensor doesn’t resolve the issue, check the wiring connections to ensure they are secure and undamaged.
If the problem persists, the control board may need to be replaced. Always consider consulting with a professional if you are unsure about performing these steps.
14. Incomplete Door Closure
Cause
Incomplete door closure is often the result of mechanical issues, which can range from misaligned door parts to accumulation of debris in the tracks.
Over time, wear and tear on the door’s hardware may cause it to lose its alignment, preventing the door from fully closing.
Besides, particles such as dust, grime, or even small objects getting lodged in the tracks can obstruct the door’s path and hinder its movement.
Solution
To solve the issue of incomplete door closure, first, check for any visible obstructions in the tracks. If found, clear away debris carefully using a soft brush or a vacuum.
If the problem persists, it may be due to misalignment. In such cases, adjusting the door’s hardware to restore its correct alignment usually resolves the issue.
However, if all efforts fail, it would be wise to seek professional help to avoid causing further damage to the door.
15. Inadequate Power Supply
Cause
The primary cause of inadequate power supply can be traced to rapid urbanization and growth in population, resulting in increased demands for electricity that outstrip the capacity of existing power infrastructure.
Also, outdated power facilities, poor maintenance, and lack of investment in the power sector significantly contribute to the issue of inadequate power supply.
Solution
Addressing inadequate power supply demands a multi-pronged approach.
Foremost, there needs to be an increase in investment in energy infrastructure, including the modernization of existing plants and the construction of new power facilities.
Further, diversifying energy sources and increasing the use of renewable energy can contribute to a more reliable power supply.
Finally, promoting energy conservation and efficient usage among consumers can help reduce the overall demand for power.
Conclusion
The interplay between various aspects discussed throughout this document underlines the complexity and interconnected nature of the topic in question.
It’s vital to understand that each factor doesn’t operate in isolation but in synergy, contributing to a larger narrative.
The insights gleaned from our exploration not only illuminate the current status quo but also provide a foundation for predicting and shaping future trends.
As we move forward, it becomes increasingly important to embrace a multidimensional perspective, considering diverse viewpoints and ever-evolving circumstances.
FAQs
What to do if the washing machine pauses?
Check if the machine is overloaded or imbalanced; adjust the load and restart the cycle.
Why does my washing machine keep pausing mid-cycle?
This could be due to an imbalance in the load. Try redistributing the clothes and start the cycle again.
Why does my washing machine keep stopping and flashing?
This might indicate a fault or error. Refer to your machine’s manual or contact the manufacturer for assistance.
Indesit Washing Machine Won T Start Cycle
How to Prevent Clothes From Getting Stuck Under Agitator
Washing Machine Will Not Agitate but Will Spin and Drain
Dryer Just Buzzes When Start Button Pushed
Kenmore Dryer Keeps Shutting Off
Miele Dishwasher Red Light Flashing
Miele W1 Stuck on Program Cancelled
Why Is My Washing Machine Pulling Threads in My Clothes
Slow Water Flow in Washing Machine
Washing Machine Drainage Options
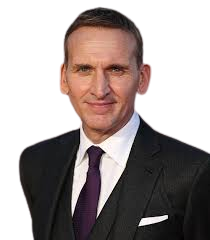
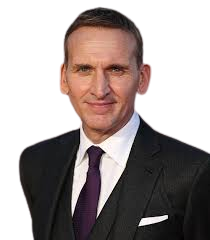
Name: Joseph Title: Owner and Founder Website: myappliancegeek.com
Biographical Info:
Joseph, the creative mind and founder behind myappliancegeek.com is a distinguished expert in the field of home appliances and technology.
Education: Joseph holds a prestigious degree in Appliance Engineering from a renowned institution in the United States, [Stanford University], where he gained a profound understanding of appliance design, mechanics, and technology.
Professional Experience: Joseph’s professional journey spans over [18 ] years in the home appliance industry. His extensive experience includes working with industry-leading appliance manufacturers, prominent retailers, and appliance repair services.
Entrepreneurship: In [2000], Joseph founded myappliancegeek.com, a platform dedicated to providing comprehensive information, advice, and solutions for those seeking guidance in the world of appliances.
Passion for Appliances: Joseph’s unwavering passion for home appliances stems from his belief in their pivotal role in improving our quality of life.
Contributions to the Industry: Joseph’s commitment to the home appliance industry is evident through his extensive writing and speaking engagements.
Community Involvement: Joseph is not only an online presence but also an active member of the community, frequently engaging in outreach programs, local workshops, and charitable initiatives.