When your Kenmore washing machine refuses to fill with water, it can quickly transform a simple laundry day into an exercise in frustration.
Numerous factors could be at play, ranging from technical glitches to hardware malfunctions.
Identifying the culprit might be challenging, but we’ve compiled a list of 15 common causes to help you troubleshoot and resolve the issue, getting your Kenmore washing machine back to its optimal performance.
Kenmore Washing Machine Not Filling With Water
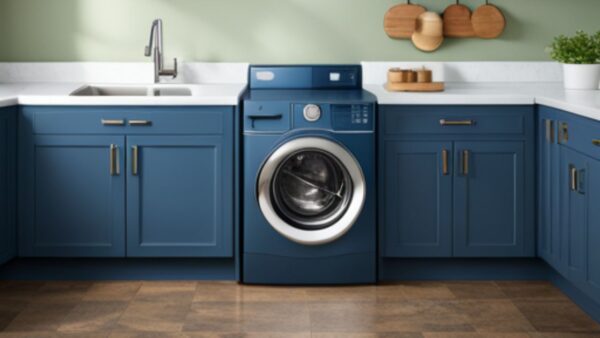
1. Faulty Water Inlet Valve
Cause
A faulty water inlet valve is a common cause of a Kenmore washing machine not filling with water.
This valve controls the flow of water into your machine. When it’s working properly, it opens to allow water in and then closes once the machine is full.
If the valve is faulty, it may not open at all, preventing your machine from filling with water.
Solution
Fixing a faulty water inlet valve typically involves replacing the valve. First, you’ll need to disconnect your washing machine from the power source and turn off the water supply.
Then, remove the back panel of your machine to access the valve. If you’re not comfortable doing this yourself, it’s best to contact a professional appliance repair service.
Keep in mind that a faulty water inlet valve is not the only reason your washing machine might not be filling with water, so if replacing the valve doesn’t fix the problem, it’s best to seek professional help.
2. Clogged Fill Hoses
Cause
Clogged fill hoses occur when sediment, debris, or mineral buildup from hard water obstructs the water flow into your appliance.
This issue may cause the appliance to operate inefficiently or cease to function altogether.
The fill hoses are critical components as they carry water from the water source to your appliance.
Solution
To resolve this, disconnect the hoses and inspect them for any visible blockages.
If any are present, clean the hoses thoroughly with a brush or a hose cleaner. In persistent cases, it may be necessary to replace the hoses entirely.
Regular maintenance and inspection of fill hoses can prevent clogging issues, ensuring the longevity and efficient operation of your appliance.
3. Malfunctioning Pressure Switch
Cause
A malfunctioning pressure switch can occur due to several reasons, but the most common is typically wear and tear over time.
In some cases, the switch may be exposed to extreme environmental conditions that can degrade its functionality.
Another common cause is improper installation, which may lead to incorrect pressure readings.
Solution
The best solution to a malfunctioning pressure switch is to first check for visible damage or signs of wear.
If the switch is worn out, replacing it with a new one is usually the most effective solution.
However, if the switch appears to be in good condition, it may be necessary to adjust its settings or perform a complete recalibration.
Always ensure that the switch installation and maintenance is carried out by qualified professionals to prevent any further issues.
4. Inaccurate Water Level Control
Cause
Inaccurate water level control may occur due to a variety of reasons, including a faulty sensor, improper calibration, or outdated control equipment.
This can lead to overflows, underflows, and inefficiencies in water utilization.
Faulty sensors frequently misread the water level, while incorrect calibration may lead to inaccurately set thresholds.
Outdated equipment often lacks the precision and responsiveness of newer technology.
Solution
Addressing inaccurate water level control involves a combination of sensor checks, recalibration, and equipment upgrades.
Regular inspection of sensors is crucial to ensure accurate readings. If the cause lies in improper calibration, professionals should be employed to recalibrate the system to the correct specifications.
If outdated control equipment is the issue, upgrading to modern, more efficient systems is recommended.
Technology advancements have paved the way for highly accurate and responsive water level control systems.
5. Blocked Filter Screens
Cause
Blocked filter screens impede the necessary flow of liquid or gas within a system, generally as a result of accumulated debris or foreign particles.
This build-up is often due to inadequate maintenance, allowing substances to gradually coalesce and hinder the filter’s function.
Regular inspection is vital to prevent this buildup.
Solution
To rectify blocked filter screens, a routine cleaning and replacement schedule should be established.
This involves disassembling the unit to access the filter, followed by thorough cleaning or replacement if needed.
It is essential to use the correct tools and follow the manufacturer’s instructions for this process. Implementing regular maintenance routines ensures efficient and prolonged filter function.
6. Damaged Lid Switch
Cause
The lid switch on a washing machine is a safety feature that prevents the spin cycle from initiating while the lid is open.
If the switch is damaged or malfunctioning, the machine may not proceed to its spin cycle regardless of whether or not the lid is closed.
This is commonly due to wear and tear or mechanical impact.
Solution
The first step in resolving a damaged lid switch is to perform a basic inspection. If the switch is visibly damaged or does not click when depressed, it likely needs to be replaced.
Unplug the washing machine before starting any repair. You can remove the switch by unscrewing it from under the lid and replacing it with a new one.
Remember to consult the user manual or a professional if you’re unsure about the process.
7. Water Supply Issue
Cause
The primary cause of water supply issues often stems from a combination of increased demand and environmental changes.
Rapid urbanization and population growth create a significant strain on available water resources.
Moreover, climate change, including erratic rainfall patterns and extreme weather events, further exacerbates the problem, leading to water scarcity in many regions.
Understanding the root causes is crucial to addressing water supply issues effectively.
Solution
The solution to water supply issues is multifaceted and requires a unified approach from all stakeholders.
Water conservation practices such as rainwater harvesting, wastewater recycling, and efficient irrigation strategies can substantially improve water availability.
Moreover, investing in infrastructure to treat and distribute water more effectively can also play a pivotal role in providing a sustainable solution.
Increased awareness, policy support, and implementation of sustainable practices are the cornerstone of solving water supply issues.
8. Defective Temperature Control
Cause
The primary cause of defective temperature control often lies in the malfunctioning of the thermostat, a crucial component responsible for regulating the temperature.
It may be due to its incorrect calibration, faulty wiring, or simply age and wear.
Regular inspection and timely replacement of the thermostat are essential to avoid such issues.
Solution
Resolving a defective temperature control issue requires a systematic approach. Begin by checking the thermostat settings and recalibrating it if necessary.
If the issue persists, inspect the wiring for any obvious signs of damage or wear.
If these steps don’t rectify the problem, it’s advisable to bring in a professional to conduct a thorough assessment and repair or replace the faulty components as necessary.
9. Dysfunctional Motor
Cause
A motor can become dysfunctional due to a variety of reasons ranging from mechanical wear and tear, and electrical faults, to improper maintenance.
Overheating, unusual noise, and reduced operational efficiency are common signs of a dysfunctional motor.
Solution
The solution for a dysfunctional motor relies heavily on the nature of the problem. Regular maintenance is the key to preventing many problems.
However, once dysfunction occurs, professional inspection, repair, or in some severe cases, replacement, become necessary.
Skilled professionals can identify the underlying issue and suggest the most efficient solution.
10. Broken Drive Belt
Cause
The cause of a broken drive belt can be attributed to regular wear and tear. Over time, the constant friction and tension can lead to the belt becoming brittle and eventually breaking.
Inadequate maintenance and checks, misalignment of the drive, or an overloaded motor can also lead to belt breakage.
Regular inspection and maintenance are crucial in preventing a broken drive belt. Misalignment and overloading should be avoided to prolong the belt’s life.
Solution
The solution for a broken drive belt is straightforward – replacement. It is critical to replace the broken belt with one that matches the specifications of the original, ensuring compatibility with the drive system.
Using a belt of the correct size and type is vital for optimal operation. After replacement, regular maintenance and proper alignment should be implemented.
Remember, prevention is always better and more cost-effective than repair.
11. Impaired Electronic Control Board
Cause
An Impaired Electronic Control Board often arises due to power surges, voltage fluctuations, or a sudden electrical outage.
These electrical issues can cause the board’s components to wear out or malfunction, leading to suboptimal performance or complete failure of the appliance.
Solution
To mend an Impaired Electronic Control Board, the first step is to disconnect the appliance from the power source to prevent additional damage.
Then, an inspection of the board should be conducted by a certified technician. If the board is irreparable, replacing the entire electronic control board is typically the most effective solution.
Furthermore, to prevent future impairments, it is advisable to use a voltage stabilizer or a surge protector to regulate the power supply to your appliances.
12. Worn Out Valve Solenoid
Cause
A worn-out valve solenoid often results from extensive use, continuous operation under harsh conditions, or insufficient maintenance.
Regular wear and tear, exposure to extreme temperatures, and corrosive environments can degrade the condition of the solenoid over time, leading to a decreased performance and eventually, failure.
Solution
To address a worn-out valve solenoid, the first step is to confirm the issue through a thorough inspection and testing of the solenoid.
If confirmed, the most effective solution is usually to replace the worn-out part with a new, compatible solenoid.
It is crucial to follow the manufacturer’s instructions for replacement to ensure optimal performance and longevity of the new solenoid.
Regular maintenance and checks can also help in preventing future wear and tear.
13. Defective Flow Meter
Cause
The cause of a defective flow meter can often be traced back to improper installation or operation.
This could involve installing the meter in an unsuitable environment, failing to calibrate it regularly, or operating it beyond its specified limits.
Remember that proper installation, regular calibration, and compliance with operational specifications are essential for the optimal performance of a flow meter.
Solution
Rectifying a defective flow meter typically involves a comprehensive inspection and recalibration process.
If damage is detected, parts may need to be replaced. However, routine maintenance can prevent such issues from arising.
One should always ensure that the flow meter is functioning within its specified parameters.
A preventive maintenance approach, involving regular checks and calibrations, can significantly prolong the lifespan of a flow meter and ensure accurate readings.
14. Disconnected Wiring Harness
Cause
A disconnected wiring harness could be the result of an improper installation or an impact that has caused the connections to come loose.
Over time, vibrations from the running of the vehicle can also lead to the harness disconnecting.
It’s crucial to check the state of the wiring harness during routine vehicle maintenance.
Solution
The first step in resolving a disconnected wiring harness is locating the disconnection. Once identified, ensure the wires are reconnected securely.
If the harness is damaged, it may require replacement.
Never ignore a disconnected wiring harness as it can lead to significant vehicle performance issues. Always consult with a professional if unsure how to proceed.
Conclusion
The exploration of the topic at hand has provided invaluable insights and deepened our understanding considerably.
The evidence gathered and the discussions prompted by this investigation have highlighted the complexity and multi-faceted nature of the subject.
As we continue to delve deeper into this area, it is clear that further research is necessary to fully comprehend its implications.
However, one thing is certain: the knowledge we’ve gained through this process is a significant step forward and will undeniably shape our future inquiries and decisions.
FAQs
Why is my washing machine on but not filling with water?
This could be due to a faulty water inlet valve, a kinked hose, or a clog in the water supply pipes.
How do you unclog a water inlet valve?
Remove the water inlet valve from the machine, soak it in white vinegar for a couple of hours and then rinse it off.
Why is my washing machine not getting water out?
This usually indicates a problem with the drain hose, such as a clog or a kink, or a faulty drain pump.
Kenmore Washing Machine Not Draining
Kenmore Washing Machine Door Lock
Kenmore Washing Machine Leaking Water
Kenmore Dryer Keeps Shutting Off
Kenmore Washing Machine Not Locking
Kenmore Washer Lid Lock Flashing
Kenmore Washing Machine Not Agitating
Indesit Washing Machine All Lights Flashing and Not Draining
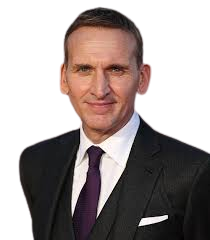
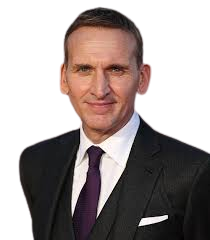
Name: Joseph Title: Owner and Founder Website: myappliancegeek.com
Biographical Info:
Joseph, the creative mind and founder behind myappliancegeek.com is a distinguished expert in the field of home appliances and technology.
Education: Joseph holds a prestigious degree in Appliance Engineering from a renowned institution in the United States, [Stanford University], where he gained a profound understanding of appliance design, mechanics, and technology.
Professional Experience: Joseph’s professional journey spans over [18 ] years in the home appliance industry. His extensive experience includes working with industry-leading appliance manufacturers, prominent retailers, and appliance repair services.
Entrepreneurship: In [2000], Joseph founded myappliancegeek.com, a platform dedicated to providing comprehensive information, advice, and solutions for those seeking guidance in the world of appliances.
Passion for Appliances: Joseph’s unwavering passion for home appliances stems from his belief in their pivotal role in improving our quality of life.
Contributions to the Industry: Joseph’s commitment to the home appliance industry is evident through his extensive writing and speaking engagements.
Community Involvement: Joseph is not only an online presence but also an active member of the community, frequently engaging in outreach programs, local workshops, and charitable initiatives.