Hi dear friends welcome to our blog. If your Kenmore Washing Machine Not Draining.
So Don’t worry this is a common issue.
In this guide, we explain 10 common reasons for this problem with unique solutions. So let’s start now.
Kenmore Washing Machine Not Draining
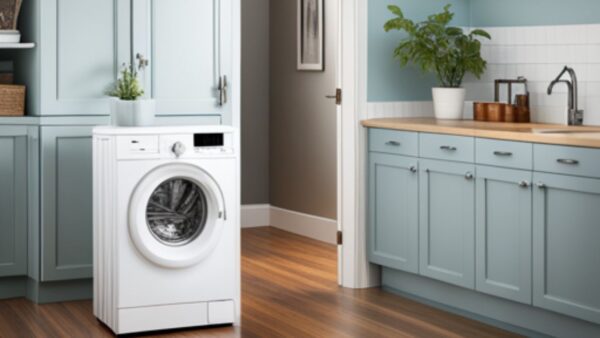
1. Clogged Drain Hose
Cause
The most common reason for a Kenmore washing machine not draining is a clogged drain hose.
The drain hose can get blocked with small items, lint, or accumulated detergent and fabric softener.
Over time, this build-up can form a blockage that prevents the washer from draining properly.
Solution
The solution to a clogged drain hose involves unplugging the washing machine, detaching the drain hose, and then cleaning it out.
You can use a long brush or a straightened wire hanger to dislodge any blockage. Always remember to check the hose for any kinks or bends.
After cleaning, reattach the drain hose and run a rinse cycle to ensure the machine is draining properly.
Always remember to wear protective gloves during this process to protect your hands.
2. Defective Lid Switch
Cause
The lid switch is a safety feature found on most top-loading washing machines.
It is activated when the lid is closed, allowing the wash cycle to commence. If the switch is defective, the machine will not start.
This is often the result of wear and tear, or damage from heavy use.
Solution
The first step in resolving a defective lid switch is to conduct a basic inspection, checking for any physical damage or loose wiring.
If the switch is visibly damaged, replacement is the only option. Remember, always disconnect the washing machine from the power supply before conducting any repairs.
If you’re unsure about this process, it is strongly recommended to consult with a professional technician or refer to the manufacturer’s guide.
3. Faulty Water Pump
Cause
The water pump may become faulty due to several reasons.
One common cause is the wear and tear of the mechanical seal, which prevents water from seeping into the bearing.
Another cause could be the corrosion of the water pump due to the continuous exposure to the coolant.
Lastly, impeller blades can break or come off due to damage or poor maintenance, leading to the pump’s inefficiency.
Solution
Fixing a faulty water pump starts with identifying the problem. If the issue is the worn-out seal, it can be fixed by replacing the seal.
However, if the pump is corroded, the only viable solution would be to replace the entire pump. In the case of damaged impellers, the impeller should be replaced or repaired.
Regular maintenance and proper use of the pump can significantly reduce the chances of these problems arising.
4. Blocked Drain Pump Filter
Cause
A blocked drain pump filter is often the result of an accumulation of small items and debris that have passed through the drum and into the pump.
This could include coins, hair clips, or even lint from the clothes.
Over time, these build-ups can prevent the pump from draining the water efficiently, leading to a blocked filter.
Solution
To resolve this, locate your washing machine’s drain pump filter – normally situated at the front bottom of the machine.
Always ensure to disconnect the machine from the power source first. Next, unscrew the filter cap and remove any visible debris.
Remember to place a towel or tray underneath the filter to catch any residual water.
After cleaning, screw the filter cap back into place, ensuring it is secure.
Always run a short wash cycle following the cleaning to ensure the blocked drain pump filter has been adequately cleared.
5. Malfunctioning Control Board
Cause
A malfunctioning control board often means that the appliance isn’t receiving correct instructions from the control panel.
This issue may stem from power fluctuations, worn-out components, or software errors.
Extended use and normal wear and tear can cause components to degrade over time, leading to malfunctions.
Solution
Addressing a faulty control board begins with diagnostics to confirm the issue. It’s advisable to consult a professional technician, who can accurately diagnose and rectify the problem.
In many instances, they might need to replace the control board or update the software. Regular maintenance and timely upgrades can prevent such issues.
6. Stuck Check Valve
Cause
A check valve might become stuck due to a multitude of factors.
Most commonly, this issue arises from a build-up of debris or sediment in the valve, structural damage to the valve components, or prolonged inactivity leading to valve parts seizing up.
These causes can disrupt the proper functioning of the valve, preventing it from opening or closing as needed.
Solution
Addressing a stuck check valve typically involves cleaning, repairing, or replacing the valve.
Cleaning can remove any buildup of debris or sediment, freeing the valve to move correctly.
If structural damage is the cause, the damaged parts may need to be repaired or the entire valve might need replacement.
Regular maintenance and periodic checks can help prevent this problem by ensuring that the valve remains in good working order.
7. Worn Out Drive Belt
Cause
A worn-out drive belt, often evident from its frayed edges or a squeaky noise, results from prolonged usage, improper tension, or poor quality of the belt itself.
The drive belt is essential for the smooth functioning of the vehicle, transmitting power from the engine to various components.
Undue wear and tear of the drive belt can lead to inefficient operation of the vehicle.
Solution
Addressing a worn-out drive belt involves its timely replacement to prevent comprehensive damage to the vehicle’s operations.
Use a high-quality belt offering durability and efficiency, and ensure it’s fitted with the correct tension to avoid premature wear.
Regular inspection of the drive belt is crucial to detect signs of wear and tear early on, allowing for proactive maintenance and thereby enhancing the vehicle’s lifespan.
8. Impaired Motor Coupling
Cause
Impaired motor coupling is typically caused by neurological disorders or damage to motor neurons, affecting the ability of muscles to coordinate movements smoothly and efficiently.
In some instances, it can also be a symptom of age-related degenerative diseases or the aftereffect of certain traumatic injuries.
Solution
A solution to impaired motor coupling largely depends on the underlying cause.
Physical therapy and rehabilitation exercises play a crucial role in restoring the coordination of muscle movements.
In some cases, medication or surgical procedures may be necessary. Innovative technologies like neuroprosthetics and biofeedback systems are also being explored for their potential to improve motor coupling.
9. Damaged Pressure Switch
Cause
A Damaged Pressure Switch is often caused by excessive wear and tear or manufacturing defects.
It is common in systems that see heavy usage, particularly in industrial or commercial settings.
Environmental factors, like exposure to harsh conditions, can also lead to a faulty pressure switch.
Always remember, that regular maintenance and inspection can help identify potential issues before they turn into significant problems.
Solution
The most effective solution for a damaged pressure switch is replacement. While temporary fixes can be implemented, a damaged pressure switch can cause unexpected system failure.
It’s essential to choose a replacement switch that is ideal for the specific system in use, ensuring compatibility and functionality.
Ensure to engage a professional for the replacement process, to maintain system integrity and safety.
10. Obstructed Coin Trap
Cause
An obstructed coin trap typically occurs when foreign objects, like coins or small toys, accidentally get washed with your laundry and become lodged in the coin trap of your washing machine.
This obstruction can hinder the proper function of the machine, leading to drainage issues and causing it to stop mid-cycle.
Common signs of an obstructed coin trap include: unusual noises during wash cycle, water not draining properly, and the washing machine abruptly stopping.
Solution
The first step to solving an obstructed coin trap is to locate the coin trap, usually situated near the bottom of the machine.
Once located, it needs to be opened and all foreign objects removed. After the obstruction has been cleared, the machine should return to normal functioning.
Remember: Always disconnect the machine from the power source before attempting any fixes. If the problem persists, it’s advisable to call in a professional repair service.
11. Broken Timer
Cause
The primary cause of a broken timer could be due to an electrical fault, such as a blown fuse or malfunctioning components.
Exposure to extreme temperature variations or humidity could also lead to timer malfunctioning. Another cause might be physical damage if the timer has been dropped or impacted.
Solution
Resolving a broken timer would primarily involve diagnosing the root cause of failure. Electrical faults can be rectified by replacing blown fuses or faulty components.
For timer issues caused by environmental factors, storing the timer in a climate-controlled environment could help prevent future problems.
In case of physical damage, the best course of action might be to replace the timer entirely or consult with a professional repair service.
Regular maintenance and careful handling can significantly increase the lifespan of the timer.
12. Failed Motor
Cause
Motor failures are often due to factors such as overheating, overloading, and lack of maintenance.
For example, motors can overheat due to excessive load, inadequate ventilation, or even environmental conditions.
Overloading occurs when a motor is used beyond its capacity, causing undue stress and potential damage.
Neglecting regular maintenance, including lubrication and periodic inspections, may lead to premature motor failure.
Solution
The key to preventing motor failure is regular preventive maintenance. This includes consistent checks for signs of wear, proper lubrication, and avoiding overloading the motor.
It’s also critical to ensure the motor is used in a suitable environment, free from excessive heat and dust, which could lead to overheating.
In case of a failed motor, it’s always best to consult with a professional for a thorough assessment and repair to ensure safe and efficient operation.
13. Disabled Spin Speed
Cause
The “Disabled Spin Speed” issue often arises as a result of a hardware malfunction.
This malfunction could be due to inaccurate calibration or a fault in the motor that controls the spin function.
It’s crucial to understand that the problem might lie in the motor controller, which regulates the spin speed. A faulty controller could prevent the system from reaching the desired speed, thus disabling it.
Solution
To address the Disabled Spin Speed issue, start by checking the calibration settings. If they’re incorrect, resetting them to factory defaults often solves the problem.
However, if the issue persists, it might indicate a motor controller malfunction. In this case, replacing the controller is usually the best solution.
Always ensure any replacement parts are compatible with your system to prevent further complications.
Remember, it’s highly recommended to consult with a professional technician to accurately diagnose and fix the issue to prevent any damage to your machine.
14. Compromised Door Lock
Cause
A Compromised Door Lock can occur due to a range of reasons. One common cause is wear and tear over time, which can lead to the lock mechanism failing.
Besides, door lock issues can arise from using the wrong key, which can damage the internal components of the lock.
Furthermore, break-ins or attempted break-ins often result in compromised door locks.
Solution
To rectify a compromised door lock, the first step should always be to consult a professional locksmith.
They can accurately diagnose the issue and suggest the most effective solution. In some cases, it might simply be a case of repairing the existing lock.
However, if the lock is extensively damaged or outdated, replacing the lock entirely might be the best course of action.
Always remember, that the quality of your door lock directly impacts your home’s security.
15. Obstruction in Drain Pipe
Cause
The root cause of obstruction in drain pipes can be numerous. Excessive disposal of grease, food scraps, hair, and non-biodegradable materials can all lead to a pipe blockage.
Over time, these substances accumulate and harden inside the pipe, preventing water and waste from flowing freely.
Solution
Effective solutions to a clogged drain pipe involve both preventative measures and action-oriented responses.
Routine cleaning, mindful disposal of waste, and periodic professional inspections can help prevent obstructions.
If a blockage occurs, manual cleaning with a plumber’s snake or hydrojetting can often dislodge the obstruction.
For stubborn clogs, it may be necessary to seek professional plumbing services.
Conclusion
It’s important to acknowledge the varied benefits of integrating technology into our daily routines.
Whether it’s enhancing our productivity, facilitating communication, or streamlining complex tasks, technology has reshaped the way we function in the world.
However, as we embrace its advantages, we must also remain cognizant of potential drawbacks such as over-dependence and privacy concerns.
The key lies in striking a balance – maximizing the benefits while mitigating the challenges.
As we navigate through this digital era, it’s clear that technology, when used responsibly, has the potential to build a brighter, smarter, and more connected future.
FAQs
Why is my Kenmore washing machine not draining?
Your Kenmore washing machine may not be draining due to a clogged drain hose or a faulty drain pump.
How do you fix a Kenmore washer that won’t drain or spin?
You can fix this issue by unclogging the drain hose, checking for any blockage in the filter, or replacing a malfunctioning drain pump.
How do I drain the water from my Kenmore washing machine?
To drain the water, locate and remove the drain hose, then allow the water to flow into a bucket or floor drain.
Indesit Washing Machine Won T Start Cycle
GE Washer Clicking Noise During Agitation
Whirlpool Washing Machine Making Loud Banging Noise on Spin Cycle
Kenmore Washer Lid Lock Flashing
washer won’t agitate makes noise
Why Is My New Whirlpool Washer So Loud
Washing Machine High-Pitched Noise
Dryer Taking Multiple Cycles to Dry
Kenmore Washing Machine Not Agitating
Indesit Washing Machine Door Lock Light On
Kenmore Washing Machine Not Filling With Water
Kenmore Washing Machine Not Locking
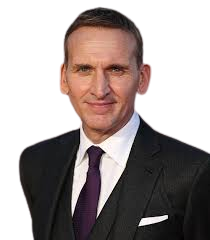
Name: Joseph Title: Owner and Founder Website: myappliancegeek.com
Biographical Info:
Joseph, the creative mind and founder behind myappliancegeek.com is a distinguished expert in the field of home appliances and technology.
Education: Joseph holds a prestigious degree in Appliance Engineering from a renowned institution in the United States, [Stanford University], where he gained a profound understanding of appliance design, mechanics, and technology.
Professional Experience: Joseph’s professional journey spans over [18 ] years in the home appliance industry. His extensive experience includes working with industry-leading appliance manufacturers, prominent retailers, and appliance repair services.
Entrepreneurship: In [2000], Joseph founded myappliancegeek.com, a platform dedicated to providing comprehensive information, advice, and solutions for those seeking guidance in the world of appliances.
Passion for Appliances: Joseph’s unwavering passion for home appliances stems from his belief in their pivotal role in improving our quality of life.
Contributions to the Industry: Joseph’s commitment to the home appliance industry is evident through his extensive writing and speaking engagements.
Community Involvement: Joseph is not only an online presence but also an active member of the community, frequently engaging in outreach programs, local workshops, and charitable initiatives.