Welcome to our discussion on GE Front Load Washer control panel problems.
We know that any issue with your home appliances, especially something as essential as your washer, can be frustrating.
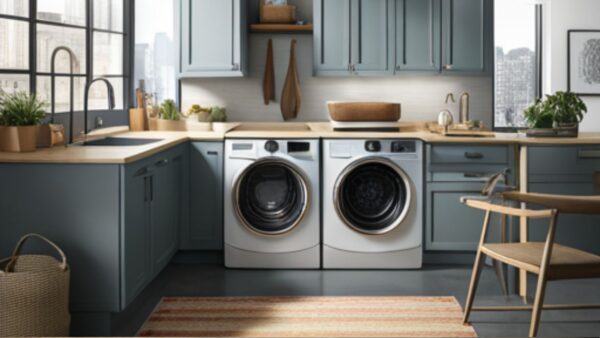
Rest assured, we’re here to help you navigate through these challenges.
In this guide, we’ll explore the top 10 problems you may encounter with your GE Front Load Washer’s control panel. With our easy-to-understand solutions, you’ll be back to smooth laundry days in no time!
GE Front Load Washer Control Panel Problems
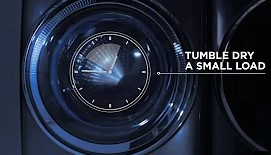
1. Failure to Start
Cause
The primary cause of a “Failure to Start” problem in your GE Front Load Washer could be a faulty door lock.
This is a safety feature designed to prevent the machine from operating when the door is not properly closed.
Other potential causes might include an issue with the power supply or a malfunctioning control panel.
Solution
Once the cause has been identified, the solution can be determined. If the problem lies in the door lock, having it repaired or replaced by a professional is recommended.
When dealing with power supply issues, check if your home’s circuit breaker or fuse box is functioning properly.
Finally, if the control panel is at fault, contact a certified GE Service representative for further assistance.
Please remember:
It is always important to ensure safety while troubleshooting appliance issues.
Make sure the washer is unplugged or disconnected from the power source before attempting any repairs, and seek professional help when in doubt.
Takeaway:
A GE Front Load Washer “Failure to Start” issue can be caused by a variety of factors including a defective door lock, problems with the power supply, or a malfunctioning control panel.
Appropriate solutions include door lock replacement, checking your home’s power supply, or contacting a certified GE Service representative.
2. Unresponsive Touch Panel
Causes
The root causes for an unresponsive touch panel can be multifarious. It could be a result of software glitches or faulty updates causing system errors.
There could also be physical damage, such as cracks or water exposure affecting the screen sensitivity.
Lastly, overloading the device with multiple applications can also cause it to become unresponsive due to system overload.
Solutions
To rectify an unresponsive touch panel, there are several steps you can take.
Firstly, if software issues are the culprit, try restarting the device or performing a factory reset (be sure to back up your data first).
In case of physical damage, consult a professional repair service.
If the issue is due to many apps running concurrently, try closing unnecessary applications or upgrading your device to one with greater processing power.
Remember, regular device maintenance can help prevent such issues from arising.
3. Inaccurate Temperature Settings
Cause
The problem of inaccurate temperature settings often stems from faulty thermostats or temperature sensors.
This can be due to wear and tear over time, incorrect installation, or even an electrical issue disrupting the signal between the thermostat and the heating or cooling system.
An uncalibrated thermostat, a malfunctioning sensor, or a disrupted signal can significantly affect the accuracy of temperature settings.
Solution
To resolve this issue, it is recommended to first check the thermostat for any visible issues such as loose wiring.
If no obvious problems are detected, consider calling a professional HVAC technician to check and possibly replace the temperature sensor.
Regular maintenance and professional check-ups are also advisable to prevent future discrepancies.
Professional intervention, periodic maintenance, and sensor replacements can rectify the problem of inaccurate temperature settings.
4. Excessive Vibration During Operation
Cause
Excessive vibration during operation often results from an imbalance in the machinery.
This could be due to irregularities in manufacturing, wear and tear over time, or sudden damage to the functioning parts.
An unaligned or loose component may also generate disproportionate forces, leading to shaking or vibrating.
Solution
To rectify the situation, it’s crucial to perform regular maintenance checks and promptly replace worn-out components.
Using vibration analysis tools can help detect any irregularities in the machine’s performance, allowing prompt intervention.
It’s also essential to ensure that all parts are correctly aligned and firmly secured to prevent unnecessary movement during operation.
5. Unexpectedly Stopping Mid-Cycle
Cause
The primary reason behind a washing machine unexpectedly stopping mid-cycle could be a malfunction within the machine’s electrical system or an issue with its water supply.
Interruptions in the power supply, faulty door locks, or even a problem with the timer can result in this issue.
If the machine senses that it’s been loaded unevenly, it may also stop to prevent damage from high-speed spins.
Solution
To rectify this issue, ensure your washing machine is properly leveled and the load is evenly distributed.
If the problem persists, it might be a more technical issue requiring professional intervention. Regular inspection and maintenance can prevent such issues.
Always remember to disconnect the washing machine from the electrical supply before attempting any fixes to avoid any accidents.
6. Failure to Drain Properly
Cause
When drainage systems fail to function optimally, a number of factors could be at play.
Often, it boils down to a blockage in the pipe system caused by solid waste, tree roots, or accumulation of grease and fat.
Improper installation or design flaws in the drainage system can also lead to inefficient drainage.
Solution
Regular maintenance and inspection of your drainage system can help detect any potential blockages or malfunctions early, reducing the likelihood of major drainage issues.
If a blockage is detected, professional plumbing services should be sought to safely and effectively clear the pipes.
In the case of design flaws, a complete overhaul of the drainage system may be necessary, requiring the expertise of a qualified and experienced plumber.
7. Inadequate Spinning
Cause
Inadequate spinning often arises due to insufficient tension on the spinning wheel or the use of inappropriate fiber for spinning.
This can result in yarn that is not durable or consistent, affecting the quality of the end product.
The key is to ensure proper tension and the use of appropriate fiber to generate a smooth and consistent spin.
Solution
The solution to inadequate spinning primarily involves adjusting the tension on the spinning wheel and choosing the right type of fiber.
Increasing the level of tension can help create a more uniform spin.
Likewise, understanding the properties of different fibers can help you select the one that is most suitable for your project. Picking the right fiber is crucial for producing strong and consistent yarn.
8. Door Lock Issues
Cause
Door lock issues are quite common and can be attributed to several factors. The most prominent causes include wear and tear, alignment problems, keyway blockages, and frozen lock mechanisms.
Excessive use over time can lead to the gradual deterioration of lock components. Similarly, misalignment of the lock with the strike plate can result in operational difficulties.
Also, the presence of debris or foreign objects in the keyway can obstruct the smooth functioning of the lock.
In colder climates, freezing of the lock system can also pose a significant challenge.
Solution
Thankfully, each of these common issues has a feasible solution. Regular maintenance and proper cleaning can prolong the lifespan of door locks and prevent wear and tear.
For alignment issues, adjusting the positioning of the door or strike plate can often resolve the problem.
A professional locksmith can effectively remove any obstructions from the keyway. In the event of a frozen lock, applying a de-icer or heat to the key before insertion can melt the ice within the mechanism.
However, it is essential to always consult with a professional for all lock-related issues to ensure safety and security.
9. Error Codes Display
Cause
The occasional appearance of error codes on your system can be attributed to various factors.
Most commonly, these codes are a result of software compatibility issues, hardware malfunctions, or network connectivity problems.
Error codes are designed as a communication tool between you and your system, providing insight into potential areas of concern.
Solution
Addressing these error codes requires a step-by-step troubleshooting approach.
For software issues, ensure that your system is updated to the latest version, and any third-party software installed is compatible with your system.
In case of hardware malfunctions, a thorough hardware diagnosis can help identify the component causing the problem.
For network-related issues, checking your internet connection or resetting your network settings often resolves the issue.
Always remember to back up your data before taking any significant actions.
10. Unusual Noises
Cause
Unusual noises often stem from mechanical malfunctions or wear and tear. They may signal issues like loose belts, faulty motor bearings, or a failing compressor.
Ignoring such noises can exacerbate the underlying issue, leading to more severe and costly damages.
Solution
The primary solution to unusual noises is an immediate, thorough inspection by a professional technician.
Prompt identification and rectification of the problem can prevent further deterioration. Regular maintenance and check-ups also help in the early detection of potential issues, ensuring the longevity of your appliance.
Conclusion
The importance of due diligence and thoughtful consideration in our actions cannot be overstated.
In every decision we make, we must weigh both the potential benefits and consequences, looking beyond the immediate scenario to consider the bigger picture.
Trustworthiness and integrity should guide our actions, shaping our approach to not only large-scale decisions but also the small, everyday choices we face.
By doing so, we not only foster a sense of trust in our relationships but also contribute positively to our personal growth and development.
FAQs
How do I reprogram my GE washer control board?
To reprogram your GE washer control board, press the ‘Start’, ‘Stop’ and ‘Power’ buttons simultaneously and hold for 3 seconds.
Why is my GE front load washer not turning on?
If your GE front load washer is not turning on, it could be due to a power issue, check if it’s properly plugged in and the circuit breaker isn’t tripped.
What are the symptoms of a washing machine control board?
Symptoms of a faulty washing machine control board may include the washer not starting, not spinning, or not draining properly.
Bosch Dishwasher Flashing Red Light
Bosch Dishwasher Keeps Asking For Salt
Indesit Dishwasher Flashing Lights 1 and 3
Dishwasher stops after 2 minutes
Lg Dishwasher Stops After 2 Minutes
Dishwasher Stops Mid Cycle and Lights Blink
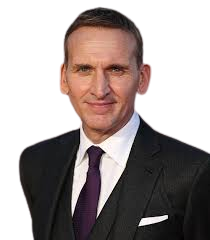
Name: Joseph Title: Owner and Founder Website: myappliancegeek.com
Biographical Info:
Joseph, the creative mind and founder behind myappliancegeek.com is a distinguished expert in the field of home appliances and technology.
Education: Joseph holds a prestigious degree in Appliance Engineering from a renowned institution in the United States, [Stanford University], where he gained a profound understanding of appliance design, mechanics, and technology.
Professional Experience: Joseph’s professional journey spans over [18 ] years in the home appliance industry. His extensive experience includes working with industry-leading appliance manufacturers, prominent retailers, and appliance repair services.
Entrepreneurship: In [2000], Joseph founded myappliancegeek.com, a platform dedicated to providing comprehensive information, advice, and solutions for those seeking guidance in the world of appliances.
Passion for Appliances: Joseph’s unwavering passion for home appliances stems from his belief in their pivotal role in improving our quality of life.
Contributions to the Industry: Joseph’s commitment to the home appliance industry is evident through his extensive writing and speaking engagements.
Community Involvement: Joseph is not only an online presence but also an active member of the community, frequently engaging in outreach programs, local workshops, and charitable initiatives.