Hi dear friends welcome to our blog. If your Maytag Bravos XL Washer Lid Lock is Stuck.
So Don’t worry this is a common issue.
In this guide, we explain 12 common reasons for this problem with unique solutions. So let’s start now.
Maytag Bravos XL Washer Lid Lock Stuck
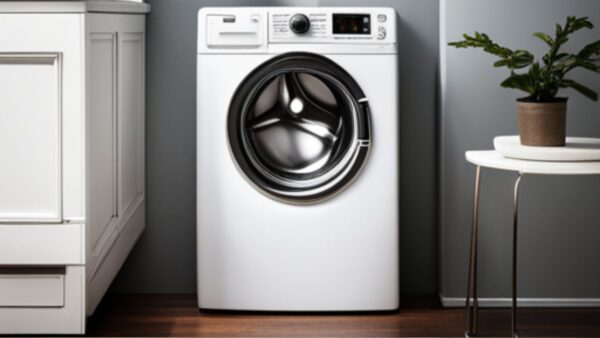
1. Faulty Lid Switch Assembly
Cause
The Lid Switch Assembly for the Maytag Bravos XL Washer is a critical component, ensuring safe washer operation by preventing the machine from spinning when the lid is open.
A faulty Lid Switch Assembly might result in the lid lock becoming stuck.
What typically happens is the switch gets jammed in the ‘locked’ position due to wear and tear, or more rarely, an electrical fault. This can halt the functionality of your washer.
Solution
The solution for a faulty Lid Switch Assembly involves its replacement. Start by unplugging the washing machine, removing the top panel, and locating the lid switch.
Once found, detach the faulty switch and replace it with a new one, ensuring it is properly connected.
After replacing the switch, plug the washing machine back in, and test its operation.
Remember, safety comes first–always unplug appliances before performing repairs, and consider consulting or hiring a professional if you are unsure about the procedure.
2. Damaged Lid Lock Mechanism
Cause
The lid lock mechanism can become damaged due to persistent use, mishandling, or manufacturing defects.
Over time, the constant opening and closing of the lid may wear out the lock mechanism, leading to malfunction.
Further, if excessive force is applied when opening or closing the lid, it can cause physical damage to the lock. In some cases, the lock may be defective from the start due to poor quality control during manufacturing.
Solution
Addressing a damaged lid lock mechanism involves either repairing the existing lock or replacing it entirely.
If the damage is minor, a qualified technician may be able to repair it. However, in most cases, replacing the lid lock mechanism is the most effective solution.
Always ensure that the replacement part is of high quality and compatible with your specific model to guarantee optimal performance.
It is strongly recommended to seek professional assistance for repairing or replacing the lid lock mechanism to ensure safety and efficiency.
3. Broken Lid Hinge
Cause
The main cause of a broken lid hinge often boils down to prolonged usage or mishandling.
Over time, regular wear and tear can gradually weaken the hinge, leading to breakage.
Furthermore, aggressively opening or closing the lid can strain the hinge, making it more susceptible to damage.
Solution
To solve this issue, you can replace the broken hinge with a new one. Ensure to purchase a hinge that matches the specifications of your product for a perfect fit.
Regular maintenance and careful handling of the lid can also go a long way in prolonging the lifespan of the hinge and preventing future breakages. Remember, prevention is always better than cure.
4. Malfunctioned Control Board
Cause
A control board malfunction can occur due to various reasons, including power surges, electrical shorts, or simply wear and tear over time.
Consistent overloading and poor maintenance practices can also contribute to the failure of the control board.
Solution
The most effective solution for a malfunctioned control board is to replace it with a new one.
It’s critical to ensure the replacement board matches the exact specifications of the original.
Regular preventive maintenance, including inspecting for signs of wear, routine cleaning, and timely repairs can help prevent future malfunctions.
Always remember to unplug any electrical device before attempting repairs to ensure safety.
5. Loose Lid Lock Wires
Cause
Loose lid lock wires can be a common issue with many appliances and are often the result of frequent use or physical wear and tear.
This can lead to the lid not securing properly and might cause the appliance to malfunction.
The primary cause of loose lid lock wires is the constant opening and closing of the lid, which exerts strain on the wires, leading to their loosening over time.
Solution
To address the issue of loose lid lock wires, it is essential first to identify if the wires are indeed loose. This can be done by carefully examining the lid lock mechanism.
Once confirmed, the loose wires can be tightened or replaced as necessary. It is recommended to get this done by a professional to ensure safety and effectiveness.
Regular maintenance and proper handling of the lid can go a long way in preventing the loosening of lid lock wires.
6. Deformed Lid Strike
Cause
The “Deformed Lid Strike” is typically caused by the improper alignment or fitting of the lid on the can during the manufacturing process.
This can occur due to machine malfunctions or errors in the production line, resulting in a deformed or misshapen lid.
The primary cause often lies in the oversight of quality control measures.
Solution
To rectify a “Deformed Lid Strike”, it’s crucial to ensure the correct and accurate alignment of the lid to the can during production.
This involves regularly monitoring and maintaining the machinery involved in the process, as well as rigorous quality control inspections to detect any anomalies early.
Investing in advanced automation and inspection systems can significantly reduce the occurrence of such production errors.
7. Obstructed Locking Mechanism
Cause
An obstructed locking mechanism often results from the accumulation of dirt, grime, rust, or even small debris within the keyhole.
This buildup can prevent the key from fitting into the lock correctly or turning smoothly, thereby impeding the lock’s proper functioning.
Solution
To address an obstructed locking mechanism, a common and effective solution is to clean the keyhole using a can of compressed air to blow out loose debris.
Following this, a small amount of graphite-based lubricant should be applied. This helps to smooth the internal mechanism allowing the key to turn more easily.
Please avoid oil-based lubricants as they can attract more dirt over time. If the problem persists, seek professional help from a locksmith to avoid causing further damage to the lock.
8. Worn-Out Lid Lock Solenoid
Cause
The Lid Lock Solenoid is an essential component in washing machines, ensuring the lid stays locked during operation for safety.
However, frequent use and time can wear it out, causing it to malfunction.
This often manifests as the washing machine failing to operate because it cannot confirm the lid is locked, triggering a fail-safe mechanism.
Solution
The most effective solution to a worn-out Lid Lock Solenoid is replacement.
This task should be undertaken by a qualified technician to ensure proper installation and to prevent any further damage to the machine.
Early detection of wear and tear on the solenoid can significantly reduce the risk of a full breakdown, so routine maintenance and inspection are crucial.
Remember, safety and efficiency in operation are paramount.
9. Inappropriate Lid Placement
Cause
Inappropriate lid placement is often a result of hurried service or lack of attention to detail.
It can lead to spillage, impairing the usability of the product, and causing inconvenience or even injury to the user.
Proper lid placement is crucial, as it not only preserves the integrity of the product but also ensures the safety and satisfaction of the customer.
Solution
Addressing the issue of inappropriate lid placement requires a two-pronged approach: thorough training and quality control.
Employees should be trained properly on the importance of correct lid placement and its impact on customer satisfaction.
Regular quality control checks should be implemented to reinforce this training and to ensure consistent adherence to standards.
By taking these steps, businesses can significantly reduce the occurrence of inappropriate lid placement, enhancing customer experience and safety.
10. Faulty Lid Lock Sensor
Cause
The faulty lid lock sensor in a washing machine is typically caused by wear and tear over time or due to an electrical glitch.
It’s a common issue that prevents the machine from moving into the spin cycle, as the machine ‘believes’ the lid is still open.
The main signs of a faulty lid lock sensor are if the machine refuses to start or if it stops mid-cycle.
Solution
The solution to a faulty lid lock sensor is usually replacing the sensor altogether.
This is a straightforward task that requires locating the sensor, usually found near the lid hinge, and replacing it with a new one.
Ensure the power is turned off before starting the replacement. Always consult with a professional if you’re not comfortable doing it yourself. Safety should always be your first priority.
11. Broken Lid Guide
Cause
The primary causes of lid breakage typically revolve around improper handling or accidental drops.
Over time, regular wear and tear can also contribute to the lid becoming frail, making it more susceptible to breakage.
Various environmental factors such as extreme temperatures may further exacerbate this issue.
Remember, the most common cause of breakage is mishandling or accidents. Regular usage also accelerates the wear and tear process.
Be mindful of the environmental conditions as they can weaken the lid structure.
Solution
Firstly, always handle with care to prevent accidental breakages. If the lid is already damaged, consider reaching out to the manufacturer for a replacement if your product is under warranty.
In other cases, you could source a compatible lid from third-party vendors. However, ensure that the new lid is a perfect fit for your container to maintain its functionality.
Handle your items with care to avoid accidents.
Utilize your warranty for replacements where possible. When buying from third-party vendors, confirm the lid’s compatibility with your container.
12. Incompatible Washer Lid Parts
Cause
Often, washing machine lid problems can arise due to the incompatibility of the lid switch or lock component with the machine model.
The washer may refuse to operate if the lid is not properly closed or if the switch that detects the lid’s position is faulty or mismatched.
This can result from using generic parts, incorrect installation, or attempting to replace components without the appropriate technical know-how.
Solution
The most reliable solution is to consult your washer’s manual and ensure that the lid component is suitable for your specific model.
If you’re not confident in diagnosing or addressing the issue yourself, it’s best to contact a professional repair service.
They’re equipped with the necessary tools and knowledge to correctly identify and fix the problem.
Remember that using the right parts and having them properly installed not only resolves the current issue but also prevents future problems, preserving the longevity of your washer.
Conclusion
It’s important to reiterate the significance of our findings in the context of our broader research goals.
The data we’ve gathered and analyzed provides a critical foundation for further investigation. This isn’t the end of our journey – rather, it’s a stepping stone towards more comprehensive understanding.
Our conclusions are rooted in rigorous scientific research, offering a platform of reliability and trust.
Let’s continue to explore with curiosity, diligence, and integrity, as the quest for knowledge never truly ends.
FAQs
How do I manually unlock my Maytag washer lid?
Turn off your washer and unplug it for a few minutes. When you plug it back in and turn it on, the lid should unlock.
How do you bypass the lid lock on a Maytag Bravos XL?
We do not recommend bypassing any safety features on your washer, it can be dangerous and potentially void your warranty.
Is there a way to reset a Maytag Bravos XL washer?
Yes, to reset, simply unplug the machine for a minute and then plug it back in.
Whirlpool Washer Stuck on Rinse
Whirlpool Washing Machine Making Loud Banging Noise on Spin Cycle
Kenmore Washer Lid Lock Flashing
My Washing Machine Smells of Stagnant Water
How to Move Stacked Washer Dryer
Why Is My Washing Machine Stuck on Rinse Cycle
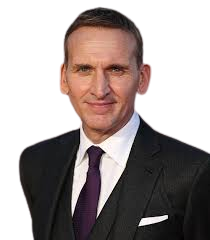
Name: Joseph Title: Owner and Founder Website: myappliancegeek.com
Biographical Info:
Joseph, the creative mind and founder behind myappliancegeek.com is a distinguished expert in the field of home appliances and technology.
Education: Joseph holds a prestigious degree in Appliance Engineering from a renowned institution in the United States, [Stanford University], where he gained a profound understanding of appliance design, mechanics, and technology.
Professional Experience: Joseph’s professional journey spans over [18 ] years in the home appliance industry. His extensive experience includes working with industry-leading appliance manufacturers, prominent retailers, and appliance repair services.
Entrepreneurship: In [2000], Joseph founded myappliancegeek.com, a platform dedicated to providing comprehensive information, advice, and solutions for those seeking guidance in the world of appliances.
Passion for Appliances: Joseph’s unwavering passion for home appliances stems from his belief in their pivotal role in improving our quality of life.
Contributions to the Industry: Joseph’s commitment to the home appliance industry is evident through his extensive writing and speaking engagements.
Community Involvement: Joseph is not only an online presence but also an active member of the community, frequently engaging in outreach programs, local workshops, and charitable initiatives.